The SARS-CoV-2 diagnostic kit is a small box containing reagents for 100 reactions. The process of its manufacture is rather laborious and takes about 5 days. We decided to show how PCR tests go from raw materials to the finished product at our manufacturing facilities located in Kyiv, on the territory of the Institute of Macromolecular Compounds Chemistry of the National Academy of Sciences of Ukraine.
Reagents from the world's leading supplier Thermo Fisher Scientific are delivered in thermoboxes, where a stable temperature below minus 18° is maintained. First, we use a small amount of material to check the quality. Only then is it possible to produce the whole shipment.
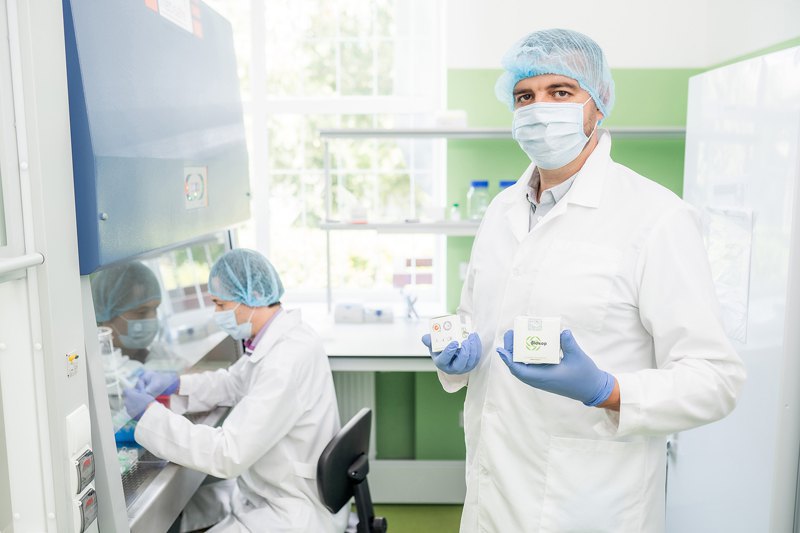
The work on the kit begins with the manufacture of a mixture of specific substances — primers and probes. This mixture plays an essential role in amplification reactions (increasing the number of particular fragments of viral RNA) and allows determining the presence of the causative agent of COVID-19 using fluorescent dyes that interact with DNA. Properly selected primers ensure specificity and sensitivity of the diagnostic kit.
In parallel, a mixture for carrying out a PCR reaction is being prepared. It contains enzymes and nucleotides that provide optimal conditions for setting up the reaction, increasing its accuracy and speed.
At the next stage, the company's specialists prepare two control samples: positive and negative. The positive control is a product of genetic engineering; it contains artificially synthesized fragments of viral genes and human RNA. Its task is to establish the operability of the reagents included in the kit.
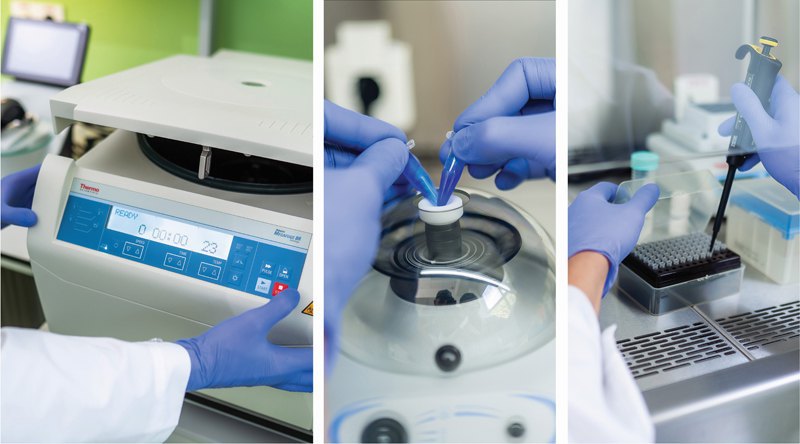
Highly purified deionized water is used as a negative control. Its primary purpose is to check the components of the reaction for the absence of DNA/RNA molecules that could have come from the external environment.
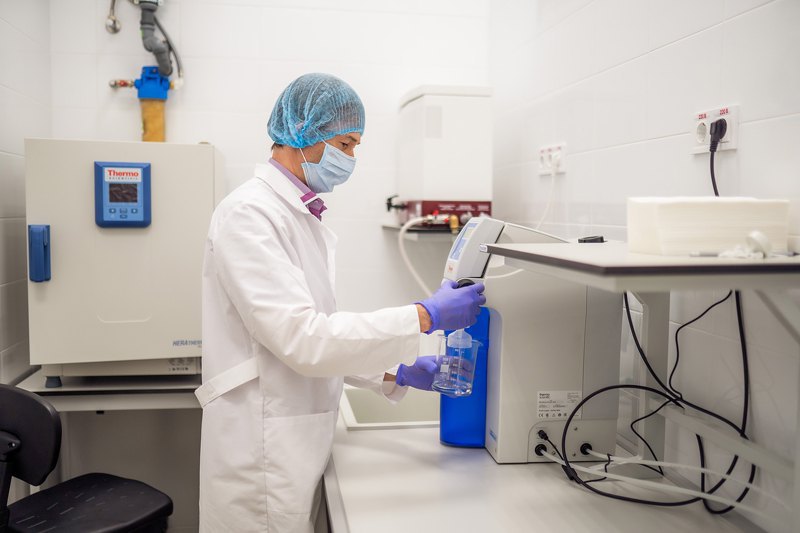
When the solutions are ready, they are dripped into test tubes with appropriate markings, the colour of lids and labels.
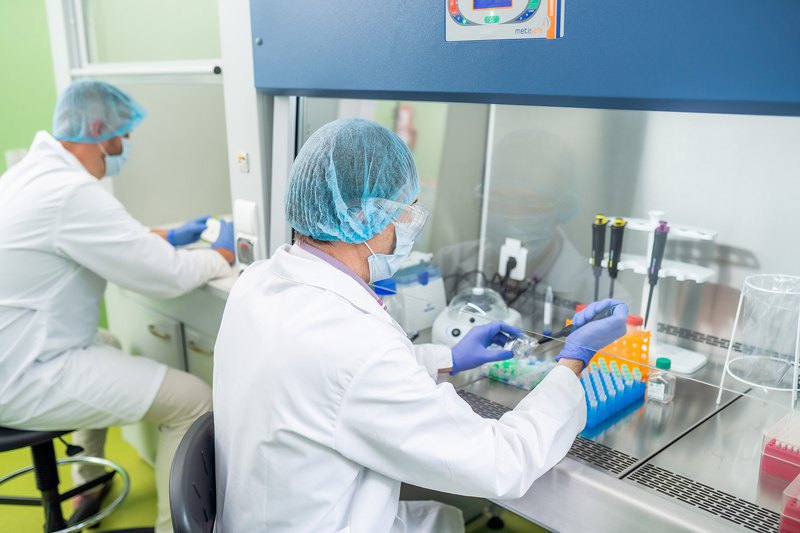
Packaged items are stored in freezing chambers at a temperature between minus 18° and minus 24°.
Samples are taken from each shipment for quality control. The company's specialists carry out the same sequence of operations as our clients do in their laboratories for PCR testing. The only difference is that in Biocor Technology the kits are tested on a synthetic copy of the coronavirus genome.
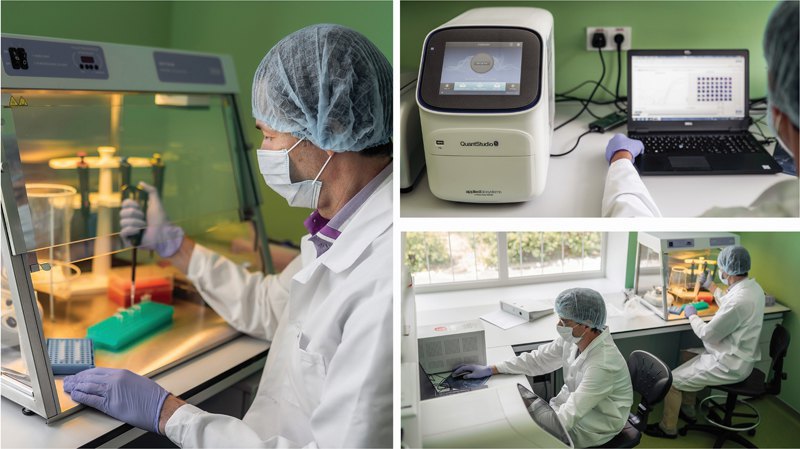
After successfully passing the quality control, the manufactured shipment of products receives a quality certificate. A sample from each shipment is stored at the enterprise for the entire shelf life.
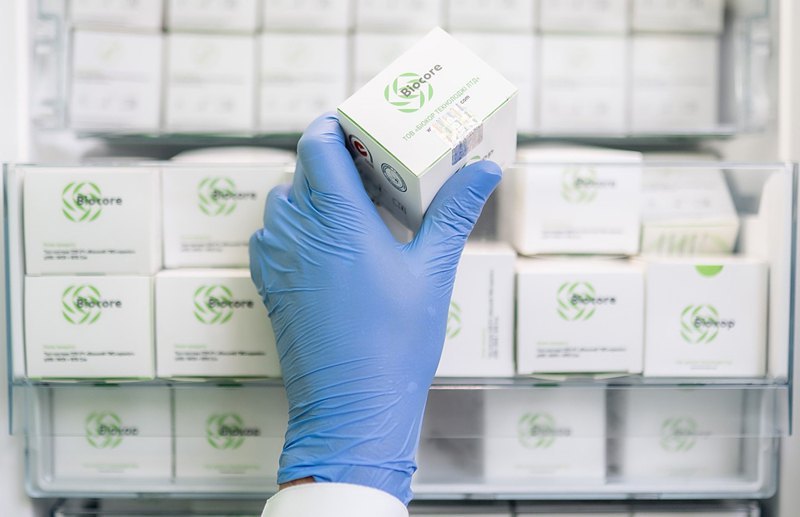
Working areas are divided to exclude accidental contamination with DNA/RNA molecules, which can be brought in even with an airflow. The ingress of such molecules leads to false-positive or false-negative results.
The required cleanliness of the manufacturing facilities is achieved by a range of special measures. Raw materials and products are transferred through special windows equipped with UV lamps for disinfecting irradiation.
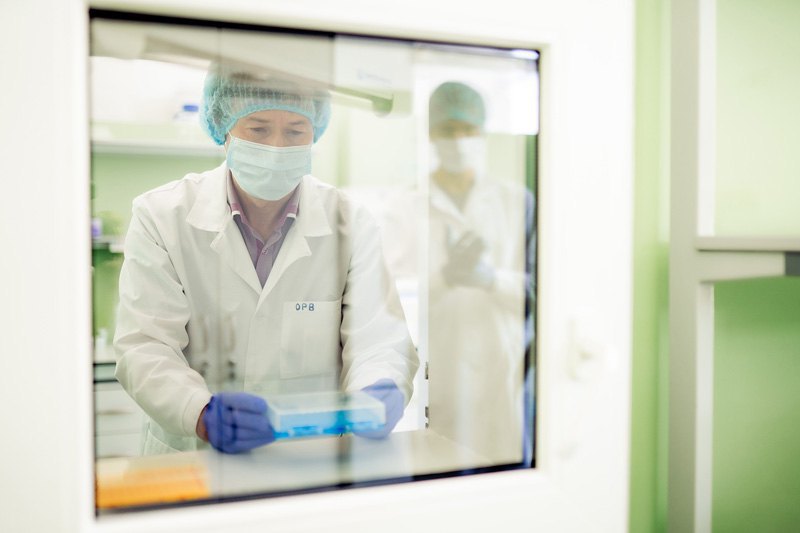
Humidity, temperature and air pressure are controlled at the production facilities. Each working zone has an independent ventilation system equipped with HEPA filters. The air undergoes three-stage purification and is disinfected by ultraviolet irradiation.
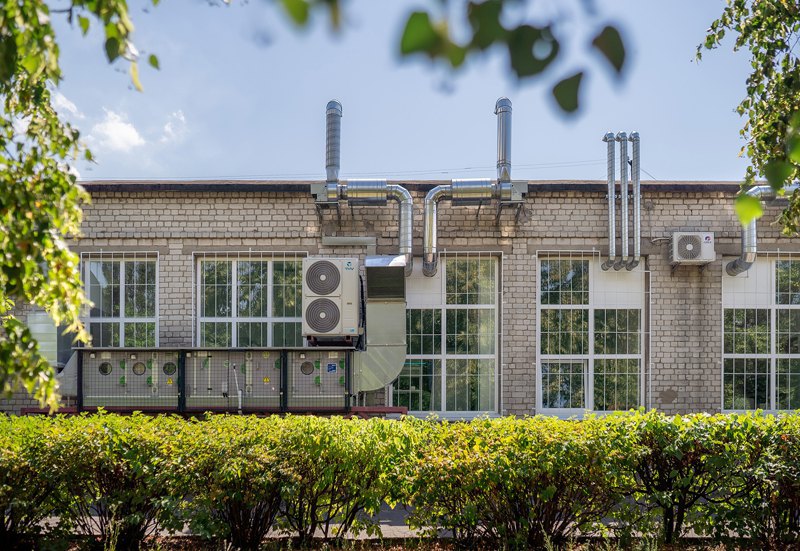
The surfaces of the working areas and PCR boxes are also subject to daily chemical and UV disinfection.
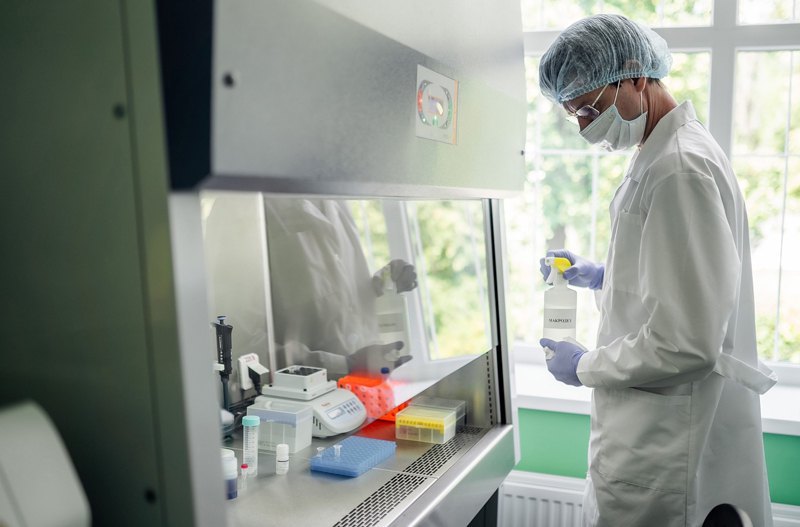
Most of the utensils and plastics used in manufacturing processes are disposable. The final decontamination of used consumables and reagents is conducted in an autoclave room.
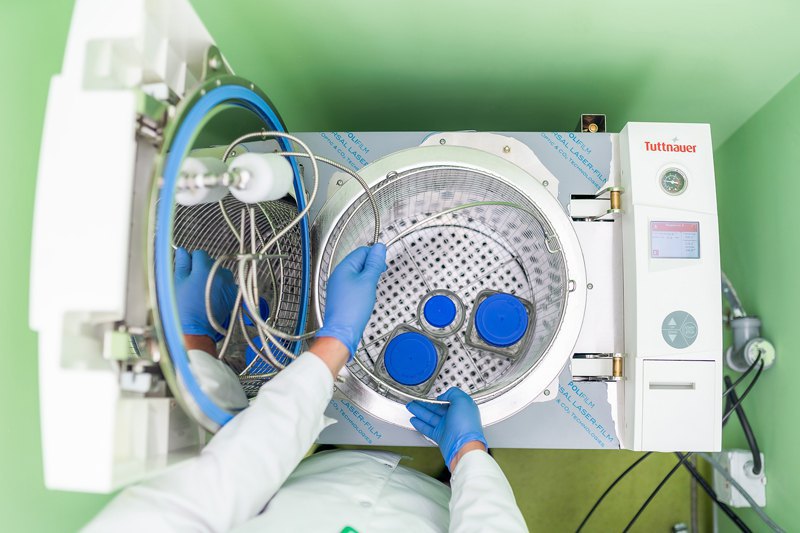
Due to the implemented quality management system, Biocor Technology can manufacture a wide range of products in three different areas — medicine, veterinary medicine and food safety. All processes are divided between zones and employees in accordance with the implemented standards ISO 9001:2015 and ISO 13485:2016.
We control and improve production, excluding any errors as much as possible, because the accuracy of diagnostics is the principle of our company.